The Practical Use and Operation of Laser Welding Machines
Introduction
Laser welding machines have become a cornerstone in modern manufacturing due to their precision, speed, and versatility. These machines use a focused beam of light to join materials with incredible accuracy, making them indispensable in various industries. This article will provide an in-depth look at the practical use and operation of laser welding machines, covering the setup process, operational techniques, safety considerations, and maintenance practices.
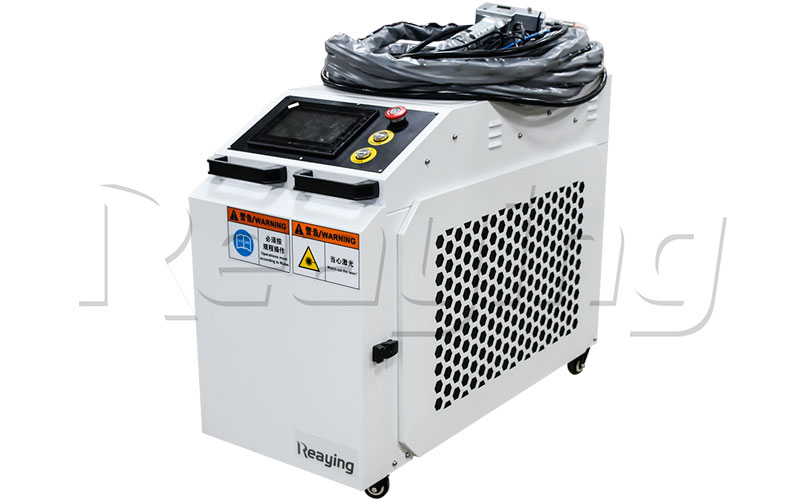
Setting Up a Laser Welding Machine
Setting up a laser welding machine involves several critical steps to ensure optimal performance and safety:
- Installation and Calibration:
- Location and Environment: Choose a location that is clean, dry, and free from dust and vibrations. The area should be well-ventilated to handle the heat and fumes generated during welding.
- Power Supply: Ensure the machine is connected to a stable power supply that matches its voltage requirements. Use surge protectors to safeguard against power fluctuations.
- Laser Calibration: Calibrate the laser according to the manufacturer’s specifications. This involves adjusting the focus, alignment, and power settings to suit the specific welding tasks.
- Workpiece Preparation:
- Cleaning: Clean the surfaces to be welded to remove any contaminants such as oil, grease, or oxides. This ensures a stronger and more consistent weld.
- Fixturing: Secure the workpieces in a fixture to maintain proper alignment and positioning during welding. This is crucial for achieving precise and accurate welds.
Operational Techniques
Operating a laser welding machine requires a thorough understanding of its controls and functionalities:
- Control Panel Operation:
- Parameter Settings: Set the welding parameters, including laser power, pulse duration, and welding speed. These settings depend on the material type, thickness, and desired weld characteristics.
- Mode Selection: Choose the appropriate welding mode, such as continuous wave or pulsed wave, based on the application. Continuous wave is suitable for deep penetration welding, while pulsed wave is ideal for delicate and precise welding tasks.
- Laser Welding Process:
- Initiating the Weld: Position the laser head over the workpiece and initiate the welding process through the control panel or a foot pedal. Ensure the laser beam is precisely focused on the weld joint.
- Monitoring and Adjustments: Continuously monitor the weld quality and make real-time adjustments to the parameters if necessary. Use vision systems or sensors to detect any deviations or defects.
- Post-Weld Treatment:
- Cooling: Allow the welded joint to cool naturally or use controlled cooling techniques to prevent thermal distortion and residual stress.
- Inspection and Testing: Inspect the weld visually and, if required, conduct non-destructive testing methods such as X-ray or ultrasonic testing to verify the weld integrity.
Safety Considerations
Safety is paramount when operating laser welding machines due to the high-energy laser beams involved:
- Personal Protective Equipment (PPE):
- Eye Protection: Wear laser safety goggles with appropriate optical density to protect against harmful laser radiation.
- Skin Protection: Use protective clothing, gloves, and face shields to guard against sparks, spatter, and UV radiation.
- Machine Safety Features:
- Interlocks and Shields: Ensure the machine is equipped with safety interlocks and protective shields to prevent accidental exposure to the laser beam.
- Emergency Stop: Familiarize yourself with the location and operation of the emergency stop button to quickly shut down the machine in case of an emergency.
- Ventilation and Fume Extraction:
- Fume Extraction Systems: Install fume extraction systems to remove hazardous fumes and gases generated during welding. This protects the operator and maintains air quality in the workspace.
Maintenance Practices
Regular maintenance is essential to keep the laser welding machine in optimal condition and prolong its lifespan:
- Routine Inspections:
- Optical Components: Inspect and clean the laser optics, including lenses and mirrors, to prevent contamination and ensure efficient laser transmission.
- Cooling System: Check the cooling system for any leaks or blockages and ensure it is functioning correctly to prevent overheating.
- Consumable Replacement:
- Nozzles and Tips: Replace worn or damaged nozzles and tips to maintain consistent welding quality and performance.
- Filters and Gaskets: Regularly replace air filters and gaskets to ensure proper ventilation and prevent dust accumulation.
- Software Updates and Calibration:
- Software Updates: Keep the machine’s software updated to benefit from the latest features and improvements.
- Recalibration: Periodically recalibrate the laser system to maintain accuracy and precision in welding operations.
Conclusion
The use of laser welding machines in manufacturing offers unparalleled precision, speed, and efficiency. However, to fully harness these benefits, operators must be well-versed in the setup, operation, safety protocols, and maintenance of these sophisticated machines. By following best practices and adhering to safety guidelines, manufacturers can achieve high-quality welds and maintain the longevity and performance of their laser welding equipment. As technology continues to advance, laser welding will undoubtedly play an increasingly vital role in diverse industrial applications.